Customer
AdipackPartner
First Bit ColombiaIndustry
Manufacturing
Country
Colombia
Product
1C:Drive
Over two decades, Adipack stands as a pioneer in manufacturing machinery tailored for the food industry. Their expertise lies in crafting state-of-the-art packaging machines specifically designed for dairy products. Alongside this flagship offering, they also develop processing equipment serving the various segments within the food industry.
Fueled by a commitment to continually enhance quality, customer service, and product excellence, Adipack's mission has been to establish enduring partnerships with their clients. Their primary focus turns around precision and care in crafting each machine, understanding that the essence of their success lies in delivering robust, reliable, and high-quality solutions to their customers.
Recognizing the crucial importance of maintaining control over the production processes, Adipack's leadership acknowledges the importance of detailed control over the manufacturing facilities. They understand that every aspect of their product depends on the nuances and dedication invested in its fabrication.
Challenges
1C:Drive
Flexible and comprehensive ERP solution capable of automating the majority of processes in companies of any size. The software combines multiple capabilities to execute various business operations, manage production workflows, digitize paper streams, and connect companies to their partners. 1C:Drive helps companies to boost their growth and help stay competitive in the dynamic business environment.
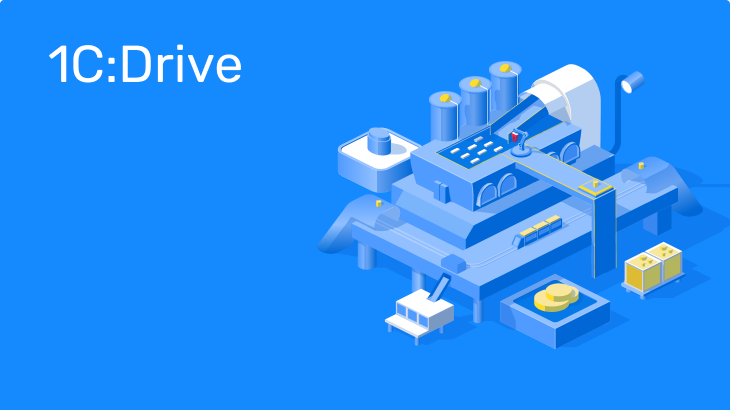
Benefits
Related Customer Stories
Interested in 1Ci solutions?
Tell us about your project and we'll find the best 1Ci partner to help.